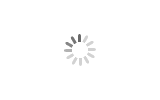
Premium Rubber Rollers conveyor belt drive rollers manufacturer
Brand Xiamen Mining
Product origin Xiamen
Rubber rollers are essential components in numerous industries, playing a critical role in processes that require a balance of pressure and gentle handling. They are essentially metal cores (sometimes wood) covered with a specialized rubber layer, offering a unique combination of resilience, durability, and adaptability. This article will delve into the diverse applications of rubber rollers, highlighting key considerations for customers across various sectors.
Applications and Customer Concerns:
1. Papermaking Industry:
Application: In papermaking, rubber rollers are used in various stages, including pressing, guiding, squeezing, and drying. Specific types include press rollers, guide rollers, squeeze rollers, couch rollers, felt rollers, and vacuum suction press rollers.
Customer Concerns:
Q: What hardness is required for press rollers?
A: Press rollers typically require a Shore A hardness of 40-95, depending on the specific application.
Q: How can I prevent premature felt damage?
A: Using press rollers with the correct hardness is crucial. Too high a hardness can damage the felt.
Q: What is the purpose of the "crown" (middle height) on a paper machine roller?
A: The crown compensates for the deflection that occurs under pressure during operation, ensuring even pressure distribution. The crown is larger for longer and smaller diameter rollers.
2. Printing and Dyeing Industry:
Application: Rubber rollers are vital for liquid pressing, dyeing, printing, and mercerizing. Examples include nip rollers, dyeing rollers, printing rollers, mercerizing rollers, hollow curved rollers, and liquid pressing rollers.
Customer Concerns:
Q: What hardness is suitable for printing rollers?
A: Printing rollers generally require a Shore A hardness of 20-50.
Q: How can I prevent "cracking" in the pattern when using a printing pressure roller?
A: Ensure the roller has the correct hardness. Insufficient hardness can lead to pattern cracking.
Q: What is the difference between active and passive rollers in dyeing?
A: Active rollers require higher hardness (98-100 Shore A) and are typically made of bakelite. Passive rollers are elastic and have a lower hardness (70-85 Shore A).
3. Other Industries:
Application: Rubber rollers find use in typewriters, mimeographs, rice hulling, leather processing, plastic embossing, metal sheet pickling, plywood pressing, and power transmission.
Customer Concerns:
Q: What are the requirements for rice hulling rollers?
A: They need to be wear-resistant, heat-resistant, and tear-resistant, with a white or light-yellow color.
Q: What are the advantages of using rubber rollers in metal sheet pickling?
A: Rubber rollers are resistant to acid, alkali, and corrosion, making them ideal for this application.
Q: What is the role of a herringbone patterned rubber roller in belt conveyors?
A: It acts as the driving component, providing a high friction coefficient (increasing power by 180%) to drive the conveyor belt.
Key Considerations for All Applications:
Hardness: The hardness of the rubber layer is a critical factor, typically ranging from Shore A 20 to 100, depending on the application.
Surface Requirements: Some applications require a smooth surface, while others need specific textures or coatings.
Middle Height (Crown): This compensates for deflection under pressure and varies depending on the roller's dimensions and application.
Media Resistance: Rollers used in liquid environments must be resistant to the specific media.
Temperature Resistance: The operating temperature range depends on the rubber compound and bonding method. Hard rubber bonding is generally limited to 70°C, while specialized adhesives can allow for higher temperatures (up to 100°C).
Manufacturing Process Highlights:
Core Material: Steel, cast iron, or copper. Hollow cores are common for larger rollers.
Rubber Layer: Can be a single layer or multi-layered (outer layer and a harder transition layer for better bonding).
Bonding: Hard rubber bonding (using ebonite) or chloroprene bonding methods are common.
Vulcanization: Large rollers are typically vulcanized in autoclaves, while smaller rollers may use plate vulcanizers.
Surface Treatment: Grinding, cleaning, polishing, and potentially coating or plating.
Conclusion:
Rubber rollers are highly versatile components used across a wide range of industries. Their ability to provide controlled pressure, coupled with their resistance to wear, chemicals, and temperature variations, makes them indispensable in many manufacturing processes. When selecting a rubber roller, it's crucial to consider the specific application requirements, including hardness, surface finish, media resistance, and operating temperature. The manufacturing process, from core preparation to surface treatment, plays a vital role in ensuring the roller's performance and longevity. By understanding these factors, businesses can choose the right rubber roller solution to optimize their operations and achieve desired results. The diameter of small rubber rollers is only 20mm, and the weight is less than 0.5kg; The diameter of large rubber rollers is 1000mm, the length is between 6000~7000mm, and the weight is up to 12000kg. The middle height of the rubber roller increases with the increase of the length of the rubber roller. The middle height of rubber rollers for various purposes is different.