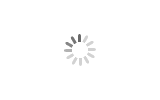
Conveyor Belt's Impact Idler belt roller conveyor systems suppliers
Brand Xiamen Mining
Product origin Xiamen
Xiamen Mining's Impact Idler offers superior wear resistance, lightweight design, and excellent corrosion resistance, ensuring durability and efficiency in harsh environments. Ideal for mining and transportation industries, it reduces material impact and energy consumption.
When it comes to belt conveyors, the loading points are often the most vulnerable. The constant impact of falling material can lead to significant wear and tear, shortening the lifespan of your conveyor belt and requiring frequent maintenance. That's where Impact Idlers, also known as Impact Rollers, play a crucial role.
These specialized idlers are specifically designed to be installed beneath the loading section of your conveyor, acting as a crucial buffer against the force of falling materials. But what exactly makes them so important, and what should you consider when choosing and implementing them? Let's delve into some common questions:
Q: What is the primary function of an Impact Idler, and where are they typically used?
A: The core function of an Impact Idler is to reduce the impact force exerted on the conveyor belt at loading points. This cushioning effect is vital for extending the lifespan of the conveyor belt. You'll typically find them installed below the loading section where material is discharged onto the belt. They are particularly essential in harsh environments like coal washeries, coking plants, and chemical plants due to their inherent resistance to corrosion.
Q: I've heard there have been improvements in Impact Idler design. What are the key advancements?
A: That's correct. Traditionally, Impact Idlers were often made by adding rubber rings to a standard steel roller. However, this method had drawbacks. For example, producing the rubber rings was slow, with a daily output of around 200 rings. Considering a single ф108*530 Impact Idler requires 26 rubber rings, producing enough for just 100 idlers would take 13 days! Furthermore, installing these rings required heating, a cumbersome process. A significant issue was the tendency for the lock nuts to loosen, causing the rubber rings to shift and fall off, leading to premature failure.
The improved design utilizes a cast rubber method. This involves designing specialized fixtures to overcome clamping issues with small diameter rollers and using casting equipment for one-time rubber coating. This significantly boosts production, with the capacity to coat over 50 rollers per day.
Q: What are the key features and benefits of these improved Impact Idlers?
A: These improved Impact Idlers, with their cold-bonded, connected elastic rubber rings and locking rings, offer several advantages. Their toughness is more than 10 times that of ordinary metal, and their lifespan is five times longer than traditional pillar supports. They are also corrosion-resistant, flame-retardant, anti-static, and lightweight, making them ideal for demanding environments, particularly in mining operations.
Q: What kind of safety features are associated with Impact Idlers and conveyor systems in general?
A: While the Impact Idler itself provides physical protection, conveyor systems often incorporate broader safety measures. These include temperature protection, where sensors near the rollers trigger a shutdown if excessive friction causes overheating. Speed protection systems detect malfunctions like motor failure or belt slippage and halt the conveyor. Additionally, coal bunker level protection uses sensors to prevent overfilling and subsequent spillage by stopping the conveyor.
Q: What should I consider when selecting and installing Impact Idlers?
A: When selecting Impact Idlers, pay attention to radial runout, flexibility, and axial movement to ensure smooth operation. Also consider the dustproof and waterproof performance, the axial load capacity, and the impact resistance of the roller. For installation, it's recommended to increase the installation density in high-impact areas and to regularly inspect and replace any damaged rollers.
Q: I understand idler spacing is important. How is the spacing for carrying Impact Idlers determined?
A: You're right, proper idler spacing is crucial for minimizing belt sag and running resistance. While experience plays a role, a more scientific approach involves calculations. For carrying Impact Idlers, the point-by-point tension calculation method is often used. The minimum tension (Smin) is related to the idler spacing (L) by the formula: Smin=(q+qd)L²cosβ/(8ymax). A simplified version, using a standard sag value, is L≤Smin/[5(q+qd)cosβ]. Factors like the material properties, belt width, conveyor inclination angle, and minimum belt tension all influence the optimal spacing.
Q: How is the spacing for the return side idlers determined?
A: The spacing for return idlers is also calculated, though the formula differs slightly: L′≤Smin/(5.3qdcosβ). Here, the belt properties and the conveyor inclination angle are the primary factors.
In conclusion, Impact Idlers are a vital investment for protecting your conveyor belt and ensuring the longevity of your system, especially at those high-impact loading points. By understanding their construction, benefits, and the principles behind their proper selection and spacing, you can significantly improve the efficiency and reduce the maintenance costs associated with your belt conveyor system.