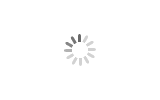
Electric Conveyor Belt Drum drive drum for belt conveyor conveyor belt drum motor
Brand Xiamen Mining
Product origin Xiamen
Electric conveyor belt drums represent a significant advancement in conveyor technology by integrating the drive motor, gearbox, and bearings directly inside the drum shell. This innovative design creates a self-contained, efficient, and space-saving drive unit for belt conveyors. This article will explore the key features of electric conveyor belt drums, address quality concerns from a production quality control perspective, and highlight their advantages in various applications.
As a type of drive drum, the electric drum uniquely combines the functionalities of driving and changing the belt's direction into a single component. Unlike traditional drive systems that require external motors and couplings, electric drums offer a compact and protected drive solution, particularly beneficial in harsh or space-constrained environments.
To ensure the reliability and performance of electric conveyor belt drums, rigorous quality control is essential throughout the manufacturing process. Let's consider some key questions from the viewpoint of a production quality control inspector:
Q: What are the critical welding points in an electric drum, and what welding defects are most concerning?
A: Critical welding points include the circumferential welds joining the drum shell to the end discs, and welds securing internal components like motor housings and support structures. "Cracks caused by incomplete weld penetration can propagate from the fusion zone, leading to weld failure". Therefore, incomplete penetration is a major concern. We must ensure full penetration welds at all critical joints to prevent structural failure, especially under high tension during conveyor startup.
Q: How do we verify the concentricity and balance of the rotating drum shell after assembly?
A: Maintaining concentricity and balance is crucial to minimize vibration and ensure smooth operation, extending bearing life. We should use precision measuring instruments like dial indicators to check runout on the drum shell surface. The tolerance should be within industry standards, ideally less than 1mm as you mentioned for end disc and drum shell alignment. Dynamic balancing tests should also be performed to ensure the assembled drum is balanced within acceptable vibration limits before installation.
Q: What are the key quality checks for the internal motor and gearbox components before drum assembly?
A: Since the motor and gearbox are integrated, their quality is paramount. Key checks include:
Motor Insulation Resistance Test: To ensure winding insulation integrity and prevent electrical faults.
Gearbox Leakage Test: To verify oil seal integrity and prevent lubricant leaks, which can lead to premature wear.
No-Load Motor Performance Test: To check motor current, voltage, and speed are within specified ranges.
Gearbox Noise and Vibration Test: To identify any abnormal noise or vibration indicating gear meshing issues.
These tests must be conducted according to relevant standards and documented thoroughly.
Q: How do we ensure the quality of rubber lagging applied to electric drums, especially adhesion strength?
A: "Rubber lagging maintenance accounts for 78% of drum maintenance", highlighting the importance of lagging quality. We must verify:
Rubber Material Certification: Confirming the rubber compound meets specified hardness (e.g., rubber hardness no less than Shore 70° for drive drums) and wear resistance requirements.
Surface Preparation: Ensuring proper cleaning and preparation of the drum shell surface before bonding.
Adhesion Strength Test: Performing pull-off tests to measure the bonding strength between the rubber lagging and the drum shell. Using "YFTOP rubber lagging with semi-vulcanized backing layer, no grinding needed, strong adhesion" can improve adhesion reliability and simplify the process.
Lagging Thickness and Uniformity Check: Verifying the lagging thickness meets specifications (e.g., rubber layer thickness often above 15mm for drive drums) and is uniformly applied across the drum surface.
Q: What are the post-assembly tests for a completed electric conveyor belt drum before it leaves the factory?
A: After assembly, comprehensive testing is crucial:
Full-Load Running Test: Operating the drum under its rated load for a specified duration to check for overheating, abnormal noise, and vibration.
Water Ingress Protection Test (IP Test): For drums designed for wet environments, verifying the ingress protection rating to ensure water and dust resistance.
Final Visual Inspection: Checking for any cosmetic defects, proper paint coating, and completeness of documentation and accessories.
Conclusion
Electric conveyor belt drums offer significant advantages in terms of integration, efficiency, and space-saving design for modern conveyor systems. However, ensuring their quality through rigorous production quality control is paramount. By focusing on critical aspects like welding integrity, concentricity, component quality, rubber lagging adhesion, and comprehensive post-assembly testing, manufacturers can deliver reliable and high-performance electric drums that minimize downtime and maximize the operational lifespan of conveyor systems in diverse industries.