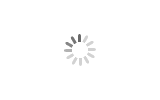
Filter Conveyor Belts: Optimizing Filtration in Diverse Industries
Brand Xiamen Mining
Product origin Xiamen
Xiamen Mining's Filter Conveyor Belt revolutionizes industrial filtration with high efficiency, large capacity, and flexibility for diverse applications, setting new standards in continuous filtering and dewatering.
Understanding the Functionality
Filter Conveyor Belts are designed to facilitate efficient filtration on belt vacuum filtration equipment. The belt, featuring strategically placed perforations, moves across a sliding table equipped with friction-reducing belts, typically made of rubber or, increasingly, PVC. The vacuum rubber filter belt itself is crafted from high-grade, wear-resistant natural rubber, reinforced with up to four layers of polyester canvas for superior strength. The belt's surface is often grooved to facilitate liquid flow during the filtration process.
Key Features and Benefits:
High Efficiency and Productivity: Filter Conveyor Belts boast high filtration efficiency, large production capacity, excellent washing results, and low moisture content in the filter cake.
Operational Flexibility: They offer flexible operation and are easy to maintain.
Chemical Resistance: Designed for chemical liquid circulation filtration processes, they are widely used in industries like PCB manufacturing, electroplating, chemical processing, leather production, and dyeing wastewater treatment.
Durability: The main body is often constructed from injection-molded Polypropylene (PP), offering exceptional durability, leak resistance, and tolerance to high temperatures and strong acids/alkalis.
Easy Maintenance: The filter material is designed for easy replacement, adapting to customer needs.
Pump Versatility: Various pump options, including self-priming pumps and magnetic drive pumps without shaft seals, can be integrated.
Enhanced Filtration: Unique internal circulation pipes and inspection ports ensure effective mixing of filter aids and carbon powder, preventing leakage and maintaining filtration quality.
Standard Equipment: Typically equipped with bottom valves, flanges, flange gaskets, PVC screws, and SUS screws.
Types of Vacuum Filter Conveyor Belts and Their Applications:
Vacuum filter belts are engineered to withstand specific operating conditions. Here are some prominent types:
Acid and Alkali Resistant Filter Belts: Ideal for environments with exposure to acids and alkalis, such as in phosphate fertilizer production, alumina processing, and catalyst (4A zeolite) manufacturing. They utilize a blend of rubber and plastic filled with acid and alkali-resistant inert materials, outperforming chloroprene rubber in acid and alkali resistance. The carcass is made of high-strength polyester canvas, and the drainage holes are made of pure rubber, effectively blocking corrosive liquids. They can be made up to 6800mm in width and 50mm in thickness.
Heat Resistant Filter Belts: Designed for filtering hot materials, with a temperature resistance ranging from 80°C to 105°C. They employ EPDM rubber for the cover, known for its excellent heat and aging resistance. A heat-resistant glass cloth can be added between the cover and the high-strength polyester canvas carcass. Pure rubber is used for the drainage holes, significantly enhancing the belt's lifespan.
Oil Resistant Filter Belts: Suitable for environments with oily materials. They feature a cover made of nitrile rubber with high acrylonitrile content and a high-strength polyester canvas carcass. This combination offers high strength, minimal deformation, and wide applicability.
Cold Resistant Filter Belts: These belts are designed to operate in temperatures ranging from -40°C to +70°C. They utilize a polyester canvas carcass, while the cover combines natural rubber and butadiene rubber, providing high elasticity, impact resistance, and cold resistance. Note that this is a different product from the previously mentioned "Cold Resistant Filter Belts" with potentially incorrect temperature rating.
Addressing Common Concerns: A Quick Q&A
Q: What is the typical lifespan of a vacuum rubber filter belt?
A: Using A-grade materials without recycled rubber can increase the lifespan by approximately 30%.
Q: What is the purpose of the grooves on the surface of the vacuum rubber filter belt?
A: The grooves facilitate the flow of liquid during the filtration process.
Q: What is the maximum width of a vacuum filter belt?
A: It can reach up to 5 meters (or specifically 6800mm).
Q: What materials are commonly used for the friction belt on the sliding table?
A: Rubber or PVC, with PVC being more prevalent in recent applications.
Q: How do I repair a damaged vacuum rubber belt?
A: Clean the area, roughen the surface, remove rubber powder, seal the leak with PVC pipe and special glue, apply a primer, and then apply a liquid wear-resistant rubber coating. It takes about 6-12 hours to cure at room temperature.
Q: What industries commonly use Filter Conveyor Belts?
A: Mining, chemical, building materials, power plants, steel mills, and aluminum plants commonly utilize these belts.
Conclusion:
Filter Conveyor Belts are essential components in various industrial filtration processes, offering a combination of efficiency, durability, and adaptability. By understanding the different types and their specific applications, industries can optimize their filtration processes, improve product quality, and minimize environmental impact. Choosing the right filter belt and implementing proper maintenance practices are crucial for ensuring long-term performance and cost-effectiveness.