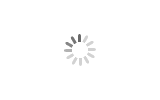
Acid-Alkaline Resistant Belts: The Reliable Solution for Corrosive Material Handling
Brand Xiamen Mining
Product origin Xiamen
In industries where conveyor belts are exposed to harsh acids and alkalis, standard belts simply won't cut it. They'll quickly degrade, leading to costly downtime and replacements. That's where Acid-Alkaline Resistant Belts come in. These specialized belts are designed to withstand corrosive environments, providing a reliable solution for transporting materials in industries like chemical processing, fertilizer production, and mining. Let's delve into the practical applications of these belts and address some key concerns from users in different sectors.
Where are Acid-Alkaline Resistant Belts Essential?
These belts are crucial in any industry where contact with corrosive substances is unavoidable. Here are some prime examples:
1. Fertilizer Production:
Scenario: Handling raw materials and finished products, many of which are highly acidic or alkaline, such as in phosphate fertilizer manufacturing.
Customer Concern: "We handle materials with varying pH levels, some as low as 0 with 10% sulfuric acid. Can these belts withstand prolonged exposure to such aggressive substances? What about the strength of the belt core?"
Answer: Absolutely. These belts are designed for this. Their covers are made from a special rubber-plastic blend filled with inert, acid and alkali-resistant materials. The core is typically made of EP (polyester) canvas, providing superior resistance to acids and alkalis compared to traditional cotton canvas. These belts can typically withstand a 10% concentration of sulfuric acid, which has a pH of 0. For higher concentrations, a specialized fluororubber belt might be needed, which can handle up to 98% concentrated sulfuric acid.
2. Chemical Processing:
Scenario: Transporting various chemicals, including acids, alkalis, and solvents, within a processing plant.
Customer Concern: "We need a belt that's resistant to a wide range of chemicals. What specific chemicals can these belts handle? What are the different classifications of these belts?"
Answer: Acid-Alkaline Resistant Belts are tested to withstand specific concentrations of acids and alkalis. They are classified into three categories based on their resistance: A1 (tested with 18% hydrochloric acid), A2 (tested with 50% sulfuric acid), and A3 (tested with 48% sodium hydroxide). The belts are typically made with a special rubber-plastic blend for the cover and EP (polyester) canvas for the core, which is stronger than the outdated cotton belts with their low 56N breaking strength.
3. Salt Production (Sea Salt):
Scenario: Conveying harvested sea salt, which is naturally corrosive, in evaporation ponds and processing facilities.
Customer Concern: "Will prolonged exposure to salt damage the belt? What about the heat from the sun in these open environments?"
Answer: These belts are built for this. Their covers are designed to resist the corrosive effects of salt. While heat can accelerate rubber degradation, the materials used in these belts, combined with proper maintenance, can withstand these conditions. The belts are also designed to be made into a ring shape to better transport materials. They can also be used with troughed belts and other related belts.
4. Paper Mills:
Scenario: Handling chemicals used in the pulping and bleaching processes, many of which are highly acidic or alkaline.
Customer Concern: "The chemicals used in papermaking are extremely corrosive. How long can we expect these belts to last in such an environment? What is the maximum speed these belts can run at?"
Answer: These belts are designed for long-term exposure to harsh chemicals. Their special rubber-plastic blend cover and EP canvas core provide excellent resistance. While lifespan depends on usage and maintenance, these belts are built to outlast standard belts in these conditions. The speed of these belts should generally not exceed 2.5 m/s.
Key Advantages of Acid-Alkaline Resistant Belts:
Superior Chemical Resistance: Special rubber-plastic blend cover filled with inert materials.
Strong and Reliable Core: EP (polyester) canvas provides excellent strength (much greater than cotton's 56N breaking strength) and resistance to acid and alkali.
Long Service Life: Designed for extended use in corrosive environments.
Good troughability and flexibility due to their special construction and materials.
Available in Various Sizes: Width can range from 100mm to 3000mm, with 1 to 10 plies, and cover thicknesses from 1.5mm to 8.0mm (working surface) and 1.5mm to 4.5mm (non-working surface).
Low elongation during use.
Questions and Answers:
Q: What is the maximum speed these belts can run at?
A: The speed of these belts should generally not exceed 2.5 m/s.
Q: How often should these belts be inspected?
A: Regular inspections are crucial, especially in corrosive environments. Look for signs of wear on the cover, any damage, and address any issues promptly. If the belt becomes misaligned, take measures to correct it. If there is any damage, make repairs immediately.
Q: How should these belts be stored?
A: They should be stored rolled in a clean, dry place, away from direct sunlight, rain, and chemicals. Maintain a temperature between 18-40°C and relative humidity between 50-80%. Rotate them every quarter.
Q: What are the technical indicators of these belts?
A: The wear is ≤ 1.20 cm³, tensile strength is ≥ 12.0 MPa, and elongation at break is ≤ 400%.
Conclusion:
Acid-Alkaline Resistant Conveyor Belts are a vital investment for industries that handle corrosive materials. Their specialized construction, featuring a robust EP canvas core and a chemically resistant cover made from a special rubber-plastic blend, ensures reliable performance and extended service life in challenging environments. By understanding the specific needs of each application and choosing the appropriate belt type (A1, A2, or A3), businesses can minimize downtime, maximize productivity, and ensure the safe and efficient transport of their valuable, yet corrosive, materials. They are a smart choice for any operation where acids and alkalis are a constant threat to equipment.