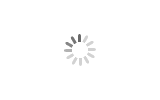
The Flame Retardant Conveyor Belt pattern rubber conveyor belt
Brand Xiamen Mining
Product origin Xiamen
In industries where the risk of fire is a constant threat, safety isn't just a priority; it's paramount. That's where Flame Retardant Conveyor Belts come into play. These specialized belts are designed to minimize the risk of fire propagation, providing a crucial layer of protection in environments like coal mines, power plants, and other industries dealing with flammable materials. Let's explore how these belts function and address the key concerns of users in various high-risk scenarios.
Scenario 1: Underground Coal Mining - The Highest Standard
Customer Concern: "In an underground coal mine, a fire outbreak can be catastrophic. We need a belt that not only resists ignition but also prevents the spread of flames. What level of protection can a flame retardant belt offer?"
Answer: For underground coal mines, Mines Fabric Core Flame Retardant Conveyor Belts are essential. These belts, often using aramid fiber as the core material, meet the stringent MT/T 914-2019 standard. They boast exceptional flame retardant properties, high strength (with a high modulus), and excellent static conductivity. The aramid core also makes the belt lighter, more flexible, and resistant to impact and tearing. They also feature low elongation and good troughability and won't delaminate. They are suitable for long-distance, high-volume, and long-span applications.
Scenario 2: Above-Ground Coal Handling - Meeting the GB10822 Standard
Customer Concern: "We operate a coal handling facility above ground. While the risk isn't as extreme as underground mining, fire safety is still a major concern. What's the appropriate belt for this application?"
Answer: General-Purpose Fabric Core Flame Retardant Conveyor Belts are ideal for above-ground operations like coal washing plants and power plants. These belts, typically using nylon or polyester canvas as the core, comply with the GB10822 standard for safety. They offer a balance of flame retardancy, durability, and cost-effectiveness. These belts are made through processes like calendering, molding, and vulcanization.
Scenario 3: Power Generation - Focusing on Specific Ratings
Customer Concern: "In a power plant, we need a belt that meets specific fire safety ratings. What ratings should we be looking for, and what do they mean?"
Answer: Look for belts with K2 or K3 flame retardant ratings. K2 limits the total burning time of six samples to 45 seconds (with no individual sample exceeding 15 seconds). K3 allows an average burning time of 60 seconds for three samples. These belts also need a static conductivity of ≤ 3 × 10⁸Ω. They must also be self-extinguishing. For cover layer, Level L requires a tensile strength of ≥14 (likely MPa) and elongation at break of ≥400%. Level D requires ≥18 (likely MPa) and ≥450%, respectively.
Key Features of Flame Retardant Conveyor Belts:
Fabric Core: Aramid fiber for underground mining (higher strength and flame retardancy), nylon or polyester for general use.
Cover Compounds: Specially formulated to resist ignition and limit flame spread.
Safety Standards: Compliance with standards like MT/T 914-2019 (for underground mining) and GB10822 (for general use).
Structure: These belts are composed of a fiber layer, an adhesive layer, a top and bottom cover layer, and an edge adhesive.
The Bottom Line:
Flame Retardant Conveyor Belts are a critical safety component in industries where fire hazards are present. Choosing the right belt, whether it's an aramid-core belt for underground mining or a nylon/polyester belt for general use, depends on the specific application and the level of risk involved. By understanding the relevant safety standards and the properties of different belt types, you can ensure the safety of your personnel and operations while maintaining productivity. These belts are your best choice when you need to transport materials in an environment that may catch fire.