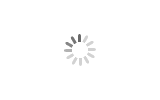
H-Type Cold-Resistant Conveyor Belts: A Quality Inspector's Guide to Crack Resistance in the Cold
Brand Xiamen Mining
Product origin Xiamen
When it comes to H-type Cold-Resistant Conveyor Belts, we're dealing with a specialized product designed to withstand not just freezing temperatures but also the stresses that can lead to cracking. So, how do we assess the quality of an H-type belt? Let's delve into the critical factors and the questions a quality inspector would ask.
What Distinguishes H-Type Belts?
H-type Cold-Resistant Conveyor Belts are specifically engineered for environments where cracking due to cold and flexing is a primary concern. They share the cold-resistant properties of other belts in the series (like the D-type), but with an enhanced focus on preventing crack formation and propagation. These belts also have good wear resistance.
Key Quality Factors for H-Type Belts:
From a quality inspector's perspective, here are the crucial aspects we examine:
Cover Rubber Compound:
Composition: The H-type, like other cold-resistant belts, likely uses a blend of natural rubber and butadiene rubber for its cover. However, the precise formulation is key. For the H-type, the compound must be optimized for crack resistance at low temperatures. The cover rubber is designed to produce a microporous carbonized layer upon exposure to high temperatures, providing resistance to burning and preventing heat transfer to the belt body.
Testing: I'd look for test data that demonstrates the cover's resistance to crack initiation and growth under repeated flexing at low temperatures (e.g., -45°C for C1 and -60°C for C2). The specific tests and acceptance criteria would be defined by industry standards, such as HG2297-92 and GB/T20021-2005 in this case. The recommended thickness of the cover rubber is 6-8mm for the top cover and 2-4mm for the bottom cover. The lifespan is also influenced by the surface temperature of the belt.
Carcass/Core Construction:
Material: High-strength polyester or nylon is typically used for the carcass. Nylon offers excellent strength (up to 700 N/mm per layer), while polyester provides better dimensional stability under load. The specific choice depends on the application's requirements. Cotton is unsuitable due to its low breaking strength of only 56N.
Adhesion: The bonding between the carcass and the cover rubber is critical. I'd look for data confirming a minimum peel strength of 3N/mm between layers, even after exposure to low temperatures. This ensures the belt remains intact under stress. The special inorganic framework used in these belts also helps prevent deformation at low temperatures.
Low-Temperature Flexibility:
Dynamic Testing: The belt should undergo dynamic flexing tests at its rated temperature (-45°C for C1 or -60°C for C2) to ensure it doesn't stiffen excessively or develop cracks. The number of flex cycles and the inspection criteria for crack detection are crucial quality parameters.
Critical Questions from a Quality Inspector's Perspective:
Q: What specific tests are used to evaluate the crack resistance of the H-type cover compound?
A: Standardized tests that simulate repeated flexing at low temperatures are used. These tests measure crack initiation and growth, ensuring the compound can withstand the stresses of cold environments. The belt should be able to withstand temperatures of -45°C (C1) or -60°C (C2).
Q: How is the adhesion between the cover and the carcass ensured at low temperatures?
A: A specialized adhesive with a minimum peel strength of 3N/mm is used. This ensures the layers remain bonded even under the stress of flexing in the cold.
Q: What is the maximum belt speed recommended for H-type belts?
A: Generally, it's recommended not to exceed 2.5 m/s to minimize stress on the belt.
Q: What are the acceptable dimensions for these belts?
A: Width can range from 100mm to 3000mm, with 1 to 10 plies, and cover thicknesses from 1.5mm to 8.0mm (working surface) and 1.5mm to 4.5mm (non-working surface).
Q: How should these belts be stored?
A: They should be stored rolled in a clean, dry place, away from sunlight and chemicals, with temperatures between 18-40°C and humidity between 50-80%. They should be rotated every quarter.
Conclusion:
H-type Cold-Resistant Conveyor Belts are a specialized solution for industries operating in freezing environments where crack resistance is paramount. As a quality inspector, I emphasize the importance of rigorous testing, particularly regarding the cover compound's crack resistance, the carcass construction, and the overall low-temperature flexibility. By carefully scrutinizing these factors and asking the right questions, we can ensure that H-type belts deliver reliable performance and longevity, even in the most challenging cold conditions. The H-type belt is a testament to the importance of quality engineering in ensuring operational efficiency and safety in extreme environments. They are a valuable investment for any operation where belt cracking due to cold is a significant concern.